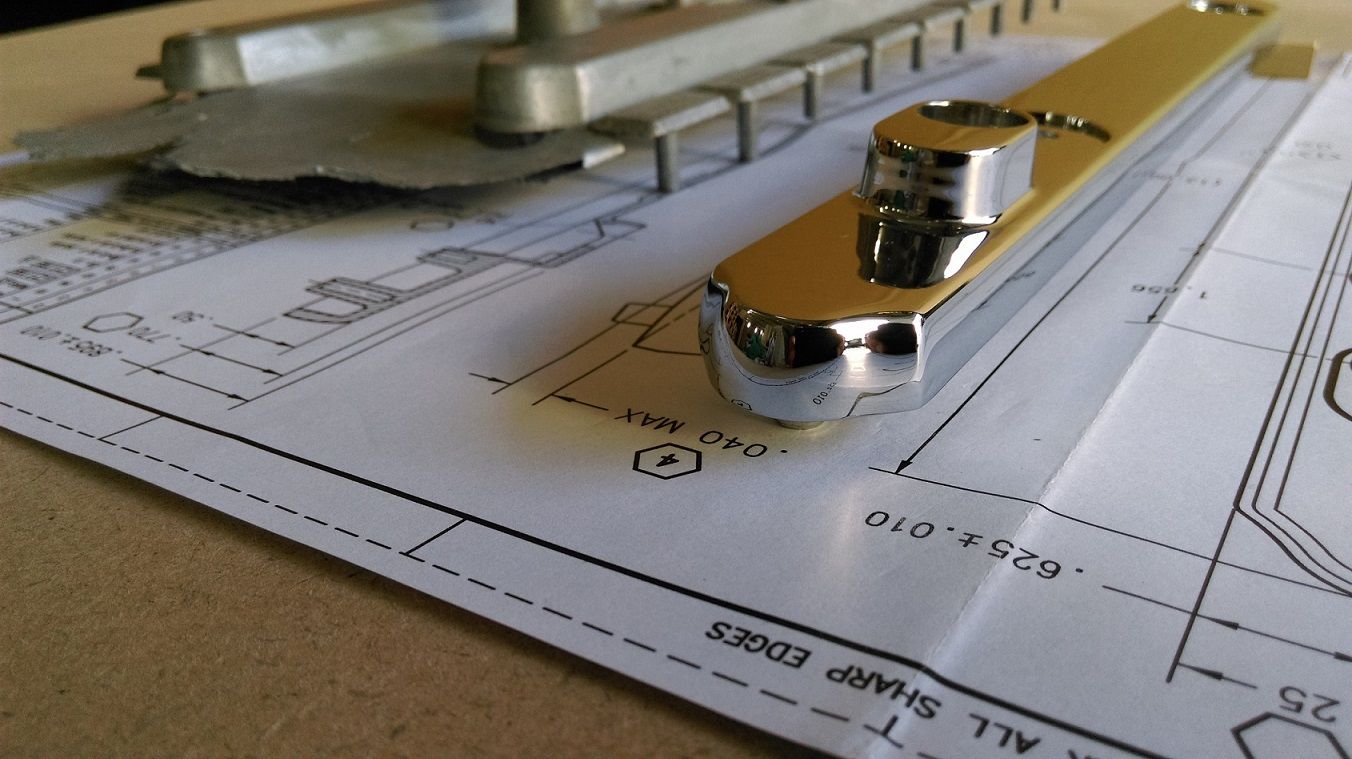
Die Casting
Accurate die casting, Die casting molding
Die casting is a highly efficient manufacturing process used to produce metal parts. It involves injecting molten metal, typically non-ferrous alloys such as brass, lead, zinc and aluminum, into a steel mold(die) under high pressure. Once the metal solidifies within the mold cavity, the die is opened, and the part is ejected, ready for further finishing if required. Key phrases typically include: die preparation, metal melting, injection, solidification, ejection, trimming and finishing.
Some of the key advantages that die casting offers include:
Rapid Production Rates: The process is highly automated and can achieve high production rates, making it suitable for mass production of parts in a short timeframe.
Cost-Effectiveness for Large Production Runs: Due to its high production rates and minimal post-processing requirements, die casting can be cost-effective for large production runs.
High Precision and Dimensional Accuracy: Die casting allows for the production of complex shapes with tight tolerances and fine details, ensuring high precision and consistency in the finished parts.
Versatility in Materials: Die casting accommodates a wide range of non-ferrous metals and alloys, offering flexibility in material selection based on specific application requirements.
Excellent Surface Finish: Parts produced through die casting typically have good surface finishes, reducing the need for additional finishing processes.
Some common applications of die casting include:
Automotive sector, electronic devices and equipment, industrial equipment, household appliances, lighting industry, furniture and hardware.